第5章 ダクタイル鉄管時代の幕明け
第5章 ダクタイル鉄管時代の幕明け
1.米国における球状黒鉛鋳鉄の発明
GHQ
ゼネラル・ヘッド・クォーター。年輩の方々は忘れもすまい、あのマッカーサー元帥の最高司令部のことである。
昭和20年8月30日、黒いサングラスにパイプをくわえて丸腰で厚木飛行場に降り立った彼の姿写真は、脳裏に焼きついたままで、消そうにも消しようがない。
以後、皇居前の第一生命ビルに本拠を構え、占領下の日本の政治、経済、教育その他一切を支配したのが、このGHQであった。
一方の日本はといえば、多くの人々が喰うに食なく、住むに家なく、働くに職なく、希望もなく、流言蜚語こそあったが諸外国の情報はまったくなく、ただただ右往左往してさまよったのであった。
そんな中で、GHQの管理下にCIE図書館というのがあった。CIEとは、Civil Information&Education Section(民間情報教育局)のことで、その図書館は情報飢餓の中にあって、アメリカ社会を伺い得る唯一の窓口なのであった。
1冊の技術誌が呼んだ春の嵐
昭和24年の春、CIE図書館の書棚に1冊の技術雑誌が現われた。
“IRON AGE”1949年2月号である。世界最大のニッケル生産会社インターナショナル・ニッケル・カンパニー(INCO)のミルス氏他2名が発表した論文が載っていた。これぞダクタイル鋳鉄(DCI)発明の衝撃的な発表であった。
実はその前年の1948年(昭和23年)5月のAFS(アメリカ鋳物協会)大会において公表されたものであるが、9ヵ月後にペーパーに載って日本にやってきたのであった。
この論文を見た日本国中の鋳鉄に関係する学者、研究者、企業の間に一大センセーションが巻き起こったのであった。その論文は簡潔なものであった。要約すると、論文の前半は「鼠鋳鉄の溶湯にマグネシウムまたはその合金を適当量加えて、鋳鉄中に残留するマグネシウムの含有量を0.04%以上とすれば、鋳鉄中の黒鉛が球状化した」というのである。
“菊の花”から“ボール”へ
そもそも鋳鉄中の黒鉛とはどこからきて、どんな役目を持っているのだろうか。ひと口に鋳鉄といっても、鉄100%でなく、種々の不純物、たとえば炭素、シリコン、マンガン、リン、硫黄、その他を含有することは先にも述べた通りで、特に炭素は鋼と鋳鉄の区別をつける主人公であることも話した。
同じ鋳鉄においても、炭素は、その量が多くなればなるほど、鋳鉄の溶融温度が低くなり、つまり湯流れがよくなり鋳造しやすくなるという大切な役目を果たしている。
そしてこの炭素は、最終的には鉄との化合物としてではなくて、大部分が黒鉛結晶として析出してくる。
では、ミルス氏らの発明、つまり黒鉛がボール状になったということが、なぜそんなに嵐のようなセンセーションを巻き起こすのか、その意義はどういうことなのかということになる。
すでに「高級鋳鉄管の開発」の項で述べたように、黒鉛の形がみみず状よりは菊の花弁状の方が鋳鉄の強度は強くなった。それをさらに追究するなら、球状つまりボールのようにするのが窮極であろう。なぜならば、同じ黒鉛量でも板状や片状よりは球状の方が表面積は最小になるからである。言い換えると、黒鉛の球状化ということは学者・技術者の長年の夢であり、理想であったのである。それが突如としてミルス氏らによって現実のものとなったので大騒ぎになったわけである。
写真11に球状黒鉛鋳鉄の顕微鏡写真の一例を示した。前に掲げた普通鋳鉄あるいは高級鋳鉄のそれとお比べいただきたい。
かくて、IRON AGE誌の論文の後半は次のように続く。「このようにして出来た球状黒鉛を有する鋳鉄は、鋳放しで毎平方ミリ当たり40キログラム以上の抗張力と3%以上の伸びを有している。よってこれを“ダクタイル鋳鉄Ductile Cast Iron”(略してDCI)と命名した」と。ダクタイルとは、延性のある、強靭なという意味の形容詞である。
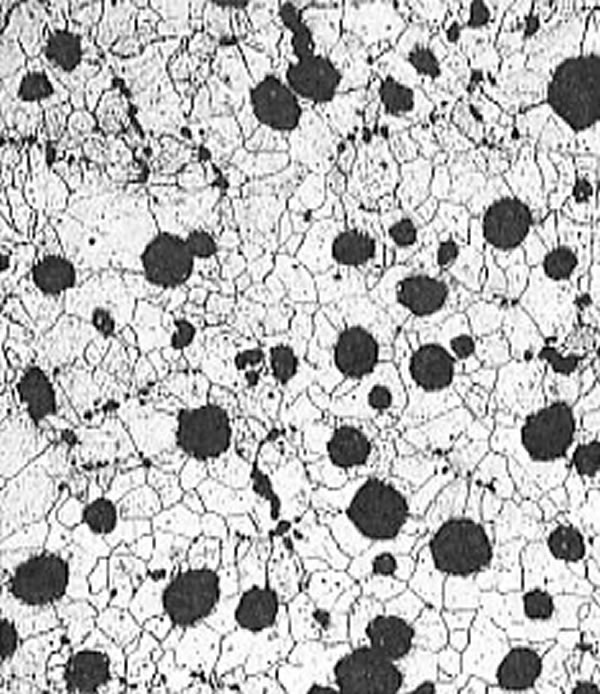
写真11 球状黒鉛鋳鉄の顕微鏡組織(100倍)
発明の動機
では次なる興味は、当然DCI発明の動機はなんであったのかということになる。昭和43年秋10月、DCIライセンシー国際会議が京都洛北宝ヶ池の国際会議場で開催された。発明者のミルス氏も初来日し、世界各国から集まった学者、研究者、経営者らから尊敬と感銘をもって迎えられた。会議は盛大で、かつきわめて友好裡に大成功を収めた。
さて、会議終了後の一日、(株)クボタはミルス氏を武庫川工場に招き懇談する機会があった。その折、若い技術者達を前にして氏の語った話の大要は次のようであった。
「アメリカでも第二次大戦中に重要基礎資源であるクロムが不足した。当時INCOはニハードと称する4.5%Ni-1.5%Cr合金鋳鉄を生産していたが、そのCr(クロム)も潤沢に使えないことになりかねないとのことから、その代替品を考えなければならないことになった。そこで、大学を出て3年目の若い冶金技術者であるミルス氏に特命された。氏はニハードのクロムに代えて、ジルコン、セリウム、ビスマス、銅、テルル、マグネシウムなどを試みる実験計画を上司に提出したが、「マグネシウムは危険だから駄目」とはねつけられたが屈せず、ついに彼の熱意に負けて「お前にまかせる」ということになった。実験は進み、ある日マグネシウムを使ったところ、爆発的な反応を起こした。飛び散った鉄の一部をひろい上げ、顕微鏡で組織を調査しているうちに黒鉛が球状化しているのを発見した」というわけであった。
思うに研究の過程においては、ちょっとした事象をついそのまま見逃してしまったり、あるいは気がついたにしても特異現象、例外的事象として顧みない例が多いものである。それを徹底的に追究したところに思いがけない大発見の機会がひそんでいたわけであり、氏の偉大さの所以もこの点にあったわけである。
(茶話)ダクタイル鋳鉄と私の出合い
昭和24年前後、私は京都大学の大学院で金属の流動性、つまり溶融状態になったときの湯流れ(鋳造性)の研究を行っていた。毎日、鉄やアルミニウムを溶解し、その成分や溶解温度を変えて、別に考案した測定器に鋳込んで、その流動性を定量的に測定することを行っていた。例のIRON AGE誌を見たのはその頃であった。早速試してみようということになった。マグネシウムの比重は1.74で鉄の7.2に比べると遥かに軽く混合させにくい。さらにマグネシウムの溶融温度は約650℃、沸騰温度は1100℃で、いずれも鉄の溶融温度よりも遥かに低い。その上、非常に発火しやすい。これはご存知のように、ひと昔前までは写真を撮るときにポッとマグネシウムの粉を発火させていた通り。つまり爆発する。その危険は十分解っているので、それなりの対策を考え、溶鉄の上にマグネシウム片を添加する瞬間に、るつぼの上から蓋をするようにして実施したが、想像以上の爆発反応が起こり、溶鉄はすべて飛び散り、サンプルをとることすらできないで、手足のやけどだけが残った次第であった。
その後、少しずつ工夫しながら試行錯誤しているうちに、ようやく丸くなった黒鉛にお目にかかることができるようになった。懐かしい思い出である。
2.鋳鉄管ダクタイル化への挑戦
ダクタイル化への挑戦
昭和24年といえば戦後の復興もようやく軌道に乗り、世情も明るさを取り戻しつつあった。美空ひばりが少女スターとしてデビュー、古橋広之進が「フジヤマのトビウオ」と活躍、湯川博士がノーベル賞を受けたのもこの年のこと。人々は「青い山脈」を口づさむまでになった。
一方では大戦の傷跡まだまだ深く、水道の世界では戦争で傷んだ管の折損も多く、昭和24年当時なお、戦災都市での漏水率は30~40%に及んでいた。それに反して人口は都市へ都市へと流入が止まらず、水需要は増大の一途を辿った。全国的に水道の拡張計画が持ち上がってきた時期でもあった。
時あたかもアメリカからDCI発明のニュースが伝わり、これこそ天恵、従来の鋳鉄管に代わって、強靭なパイプの製造に利用できないかと直感的に閃いた人がいた。(株)クボタの副社長田中勘七氏もその一人であった。氏は早速鋳鉄管部門に対し、ダクタイル管の試作を指示した。そして手さぐりのまま堅吹法、砂型遠心力法、金型遠心力法などあらゆる方法で試作が始まった。
昭和26年9月9日、サンフランシスコで日米の平和条約が締結された。間もなく和平回復後の定期飛行便の第一便が羽田を飛び立ったのであったが、田中氏はすでにその機上にいたのである。そしてINCO本社を訪問し、DCIをパイプに利用することの可否を研究者たちと議論し、確信を得て、早速特許の交渉を始めている。
このとき、すでにダクタイル管の開発に社運をかける決断で臨んでいたのであった。
ダクタイル鋳鉄(DCI)の特許
INCOはいち早く全世界の主要国に特許を申請していた。日本で特許が成立したのは昭和26年である。
これを許諾するについては厳しい条件を加え、たとえばある一定以上の試験設備を現有していること、また、ある一定数以上の専任研究者が在籍していることなどをいちいちINCOの代理人が現場調査のうえ、厳選するほどの慎重さであった。
こうして昭和27年の末頃から28年にかけて7社が供与された。それはクボタ、東芝、トヨタ自動車、日立製作所、新三菱重工、豊田自動織機および三菱造船であった。その後、時間をかけて逐次追加されている。
乗り越えねばならなかった難関の数々
先般ある親しい人から率直な指摘をいただいた。「ダクタイル鉄管はアメリカから特許を買ってきたのだから、なにも苦労なんかなかったのじゃないの?」と。
それを聞いて私は「ハッ」と気付いた。これは我々が迂闊だった。説明が足りなかった。PRが足りなかったなと反省させられたのだった。
確かに製品特許であればすでにでき上がった製品があり、その作り方、扱い方のノウハウがついており、その通りやっておれば間違いない、勝手なことすれば却って特許に反するというのが一般通念であろう。
ところがINCOのDCI特許は、あくまで基本特許であり、極端ないい方をすれば、黒鉛が球状化した鋳鉄の顕微鏡組織そのものが特許であり、特定の製品、つまり管であろうと、機械鋳物であろうと、自動車部品であろうとなんでもよい、どんな作り方でもよい、兎に角マグネシウムまたはその合金を使ってDCI「黒鉛が球状化した鋳鉄」を作れば特許にかかりますよ、ということである。
裏返せば、特定の製品をつくるノウハウは一切ついていない特許である。したがって作る側で一つ一つ暗中模索、試行錯誤、理論究明をしてかからねばならなかった。すべてがまさに未知との遭遇にほかならなかった。さればこそ幾多の危険もおかし、言い知れぬ苦難をも乗り越えねばならなかったわけである。
(1)添加合金の選択
INCOはNi-Mg(ニッケル20%-マグネシウム50%)を使ったようであるが、当時ニッケルはトン当たり数百万円もする金属で、とてもやすやすと使えるものではない。鉄-シリコン-マグネシウム合金も考案されたが、やはり危険も伴うが純マグネシウムがもっとも経済的という結論になった。
(2)原料銑鉄の厳選
原料銑については処女性ということが問題になり、できるだけ不純物の少ない銑鉄を使わないとなかなか黒鉛が球状化しない。だから当初などはスウェーデン木炭銑を使って実験をしていた。しかし工業生産となると価格、量ともに不適格である。結局、有害な不純物の限界を規定した特別な“ダクタイル銑”なるものを高炉メーカーに作ってもらって、専らこれを使用した。もちろん普通銑よりは高価である。
(3)黒鉛の球状化を阻害する元素
それは何と何かを特定することが、また大変な根気のいる研究作業であった。
一番の悪者は硫黄である。普通の銑鉄中には0.08~0.1%含有されている。これを脱硫工程といって、一般には窒素ガスでカーバイド粉を溶湯中に吹き込み硫化窒素の形で分離除去して、少なくとも0.005%以下にはしておかねばならない。
そのほかに悪戯をする元素は、アルミニウム、チタン、鉛、砒素、アンチモン、ビスマス、ジルコン、テルル、錫等々数多いが、いずれも0.00数%以下に抑えた原料を使わねばならないことが次第にわかってきた。
(4)マグネシウム(Mg)の添加方法
さて合金を使えば反応が穏やかで、確実、安全であることはわかっていても経済性からいえば純Mgが良いことまでは先述の通りわかったが、なにしろ危険な金属なので安易に扱うわけにはゆかない。Mgの融点は650℃、気化温度は1100℃、比重は1.74。しかも、昔からおなじみの写真のフラッシュに使われていたことからもわかるように、きわめて発火しやすい金属である。一方の湯(溶けた鉄のこと、溶湯ともいう)の温度は、低くても1450℃はある。したがってMgを溶湯の上に不用意に投げ込んだりすると爆発的な反応で危険極まりない。そこでいくつかの方法が試みられた。
取瓶の底にポケットを設けてMg塊を敷き、上から湯を注ぐ方法、黒鉛製または鉄板製の孔あき籠にMgを詰め込み、棒の先に取り付け、取瓶蓋の真中に設けた孔にさし込んでおき、取瓶に湯が溜められた時点で蓋をして棒を湯の底まで押し込む方法など各種の工夫が試みられた。
それぞれ一長一短あるが、鉄管のように大量連続生産するのに適した方法として圧力添加法というのが考案されて実用されている。高圧下では物質の蒸発気化温度が上昇するという一般物理現象を利用したもので、取瓶を高圧容器にしておき、溶湯が溜められた時点で窒素ガスを封入、Mgの気化温度を溶湯の温度近くになるように雰囲気の圧力を調節してやるのである。そのうえでピストンの先に取り付けておいたMgの塊を揚の中に押し込んでやれば、密閉容器内で反応は静かに進むという仕掛けである。
(5)
以上のほかにもまだまだ解決しなければならなかった問題は多くあったが、それら要素技術とその組み合わせを一つ一つ綿密に、ちょうど乱麻をときほぐすようにして解決していったのである。その間には危険も伴い、失敗もあり、事故も起こし、神経をすりへらすような長い苦しい道のりであった。
砂型遠心力鋳造の挫折
前述の各要素技術の追及と併行して、絶えず各種の方法でのダクタイル鉄管鋳造が試みられた。まず砂型遠心力鋳造である。なぜならば、この方法は昭和10年、満州久保田鋳鉄管(株)で初めて採用されて以来、FC管鋳造の長い歴史と伝統ある技術であるからである。ところが結果は完全な失敗に終わった。
この方法では金枠の内面に30~50mmもの鋳物砂を内張りし、回転させておいて一端から鋳込む。注がれた溶湯は、型に接した面、すなわち管の外面からゆっくり凝固し始め、順次内面の方に向かって固まっていく。したがって全体が固まるまでには相当の時間がかかる。
一方マグネシウム処理した溶湯は酸化しやすく、かつ固まるまでの時間が長いとマグネシウムが蒸発して消えるので、効果がなくなる性質がある。案の定、でき上がった管の内面側は黒鉛の球状化が不十分であり、かつ酸化のために皺が生じて、とてもりっぱな管とはいえなかった。
3.ダクタイル鉄管の誕生
竪型ダクタイル鉄管の成功
そこで、まったく転換した発想の遠心力管を新たに開発することになった。だが、一朝一夕には無理な話で、相当の時間を覚悟しなければならない。
ところが水道を取り巻く環境情勢は急を要しており、とても悠長なことはいっておれない。
そこでもうひとつの鋳造法として竪型(竪吹きともいう)鋳造法があった。これこそ昔からFC管でやってきた安定した方法であり、すでにダクタイルでの試作で昭和28年頃までに一応の成功をおさめていた。ただ欠点としては肉厚が厚く、重量が重い。管長も4mが限度で、遠心力管のように6mものは困難である。しかし強度は十分ある。なぜなら竪型鋳造法では外型と中子の隙間に溶湯を鋳込むので、凝固は管の内面側からと外面側からとが同時に始まって速く進行するので、マグネシウムの酸化あるいは蒸発消失もないからである。
会社としては、新規の遠心力鋳造法の開発は武庫川工場で、一方の竪型鋳造の完成は尼崎工場でそれぞれ担当するという両面作戦を展開していたのであった。
(茶話)消防車
尼崎工場で1350mm管を初めて鋳造したときのことである。朝から手順の打ち合わせや段取りにかかり、鋳込みが夕刻になった。前工程が脱硫作業であるが、カーバイド粉を窒素ガスで数分間にわたって吹き込むので、反応生成物の黒煙が高い建屋の天井から吹き上げる。続いてマグネシウム処理の工程である。反応が激しく、物凄い閃光がパッパッと天窓のガラスを真赤に染める。たまたま尼崎消防署員が望楼の上から望んでおり、「クボタが火事や!」というので数台の消防車がサイレンを鳴らしながら工場の中へ飛び込んできた。「火事はどっちだ!」と消防士。「え-、火事?どこの?」と門衛。騒ぎのあと「そんなことするんなら、事前に連絡せんかいな」と叱られ、「えらいすんまへん」と平謝りの一幕であった。
阪神水道企業団の勇気ある決断
その頃、阪神上水道市町村組合(のちの阪神水道企業団)では、第二期淀川導水路計画が具体化、そのうち尼崎浄水場から甲東ポンプ場への約6.6km強、そこから甲山浄水場までの2.8kmの区間は高圧となり、従来の鋳鉄管では耐え得ないと判断され、たまたま完成したばかりの竪型ダクタイル鉄管に着目された。
若い技術者を毎日のように工場に派遣され、抜き取った試作品を切り刻んでは機械強度試験、残留応力の有無、継手の水密試験など、考えられるあらゆる面から綿密かつ徹底的な調査・試験を実施された結果、口径1350mm管を4.1km分、口径1200mm管を1km分それぞれ初採用、昭和29年春から工事が開始された。
これが歴史を飾る日本におけるダクタイル鉄管の第1号であり、しかも世界における最初の大口径ダクタイル鉄管であった。
思えば、初めての新しい製品を、初めて採用されるということはきわめて重い責任であったはずであり、当時の阪神水道企業団の優れた先見性と勇気ある決断に、深い敬意と感謝をささげたい。
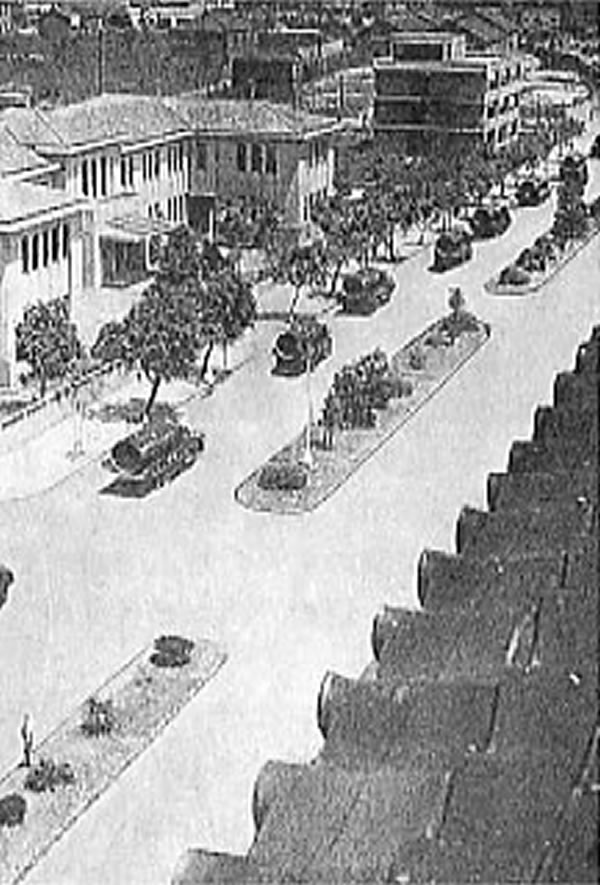
写真12 阪神水道企業団へ口径1350mm
ダクタイル鉄管を運ぶトラックの列
サンドレジン型遠心力鋳造ダクタイル鉄管の成功
先に砂型による遠心力鋳造が失敗したことを述べたが、それからすぐに新技術開発に取り組んだ。戦後、珪砂にフェノール樹脂を混合して造型する方法が実用化されつつあった。フェノール樹脂は熱硬化性といって、熱を加えるとある温度で軟化し、のちに硬化する性質がある。この特性を利用して、予熟した金枠の内面に1~2mmほどの薄いコーティングを施し、これを用いてダクタイル鉄管を遠心力鋳造することを考えた。これをサンドレジン遠心力鋳造法と呼ぶことにした。従来の砂型遠心力鋳造法に比べ、砂の層が極端に薄いため、鋳込んだときの溶湯の冷却が遥かに早い。したがって酸化物の生成がなく、管内面に皺ができる暇も与えない。ところが一方では、鋳造の常識として、急冷すれば硬くて脆い組織(セメンタイト、Fe3C)になってしまうので、鋳造後に焼鈍(ナマシ)をしてやらねばならない。
つまり950~1000℃で40~60分ばかり加熱して熱処理をするわけである。こうすればセメンタイトは熱分解して組織が変わり、強靭な鉄基地(Fe、フェライト)と球状黒鉛(C)になる。つまりダクタイル鋳鉄管ができるわけである。焼鈍は1本1本やっているわけにはいかないので、長さ50~60mの連続炉を築き、加熱、保温、冷却の各ゾーンを管が回転しながら連続的に動いていく仕組みになっている。温度管理に細心の注意が必要であることは論をまたない。こうしてサンドレジン・ダクタイル鋳鉄管の鋳造に成功したわけであるが、振り返って見れば、ダクタイル鋳鉄とはなんとむずかしい製品なのか。ここへくるまでに7年の歳月を要したことになる。
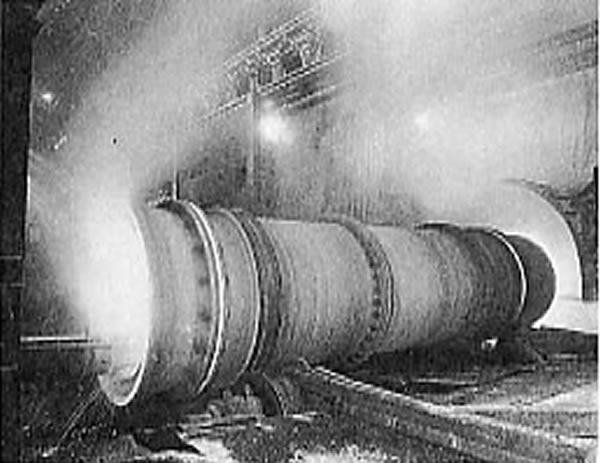
写真13 サンドレジン遠心力鋳造
桂沢水道企業団の英断
昭和31年、これまで積み上げてきた全ノウハウを注ぎ込んで、新しい生産ラインを建設することに取りかかった。
時あたかも、桂沢水道企業団(当時の桂沢上水道組合)の創設水道建設に当たり、このサンドレジン・遠心力ダクタイル鉄管採用の話が固まり、昭和31年12月、桂沢ダム取水点から浄水場までの700mm導水管、延長約4km分、続いて昭和32年7月には浄水場から唐松分水に至る700mm送水管約5.7km分の発注があった。一方クボタでは遠心力ダクタイル鉄管工場の建設はもちろん初めてのことであり、やや難渋し、やっと製品が出荷できるようになったのは、昭和32年の夏の頃であった。北海道では冬には早く雪が降って工事ができなくなる恐れがある。一方、年内通水は至上命令であった。お投所はじめ関係者の必死の努力で、全管の埋設が終わり、通水したのがなんと雪の中、御用納めの日のことであった。
これが遠心力ダクタイル管路の第1号となった。
世上初めての新製品を採用された桂沢水道企業団のご英断こそが、遠心力ダクタイル鉄管誕生とその後の研鑽の記念すべき原点となった。
ダクタイル鉄管の日本水道協会規格制定
昭和34年、第28回総会においてダクタイル鉄管の規格化が決議され、昭和35年5月に第1回専門委員会が開催された。
当時、国富日本水道協会理事長のもと、委員長は東大名誉教授三島徳七先生、副委員長は東京都の藤田博愛先生、学識経験者として、京大教授森田志郎先生と鋳物協会会長田中勘七先生であった。委員は竹中正穎氏(横浜市)、海老原三好氏(神奈川県)、渡辺清則氏(名古屋市)、芦田秀夫氏(京都市)、太野垣俊彦氏(大阪市)、多田彰氏(大阪府)、松下保男氏(神戸市)、曾原良宗氏(阪神水道)、河井貞一氏(クボタ)、武藤千秋氏(栗本)であった。日本水道協会は大西技術部長、石田規格課長および富谷技師が担当された。いうまでもなく三島博士はMK磁石の発明者として世界的に著名な鉄鋼冶金の泰斗、森田博士は鋳造学の大家であり、私の恩師でもある。田中博士は(株)クボタの元副社長で、高級鋳鉄管や遠心力鋳造の開発者として水道界になじみの深い人で、のちに田中・河井両氏の名で、「ダクタイル鋳鉄管製造法の研究開発」の功で大河内記念賞を受賞されている。委員および事務局の諸先生方は、今さら紹介申し上げるまでもない錚々たる大先達ばかりであった。
この委員会は当時の時代背景もあって、希望に溢れた白熱の論議がかわされ、翌年4月までの1年間に7回開催され、提出審議された資料数は実に90件に及び、その間に製造工場の調査や管埋設実験現場での調査などもあり、きわめてエネルギッシュなものとなった。
審議内容の詳細は割愛するが、昭和36年にJWSA G105(直管)およびG106(異形管)として公布された。口径は200~1500mm、継手の種類はA、BおよびCの3形式となっている。
なお、昭和40年の改正で口径75、100、150mmが追加された。
その後昭和49年にはJIS G5526(直管)およびG5527(異形管)となった。
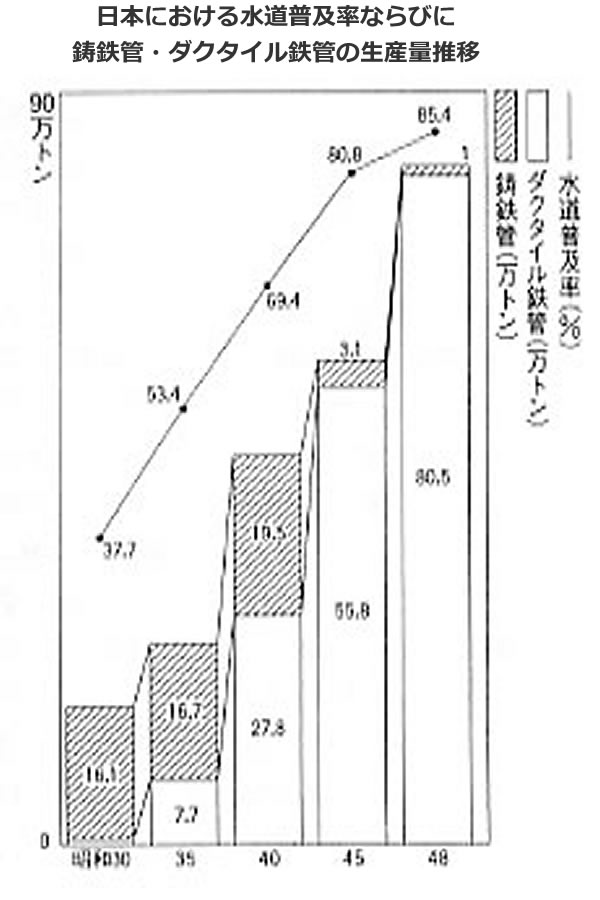
(参考) 昭和30年度~48年度の間の日本の水道普及率ならびに鋳鉄管からダクタイル鉄管への移行傾向を下の図に示した。